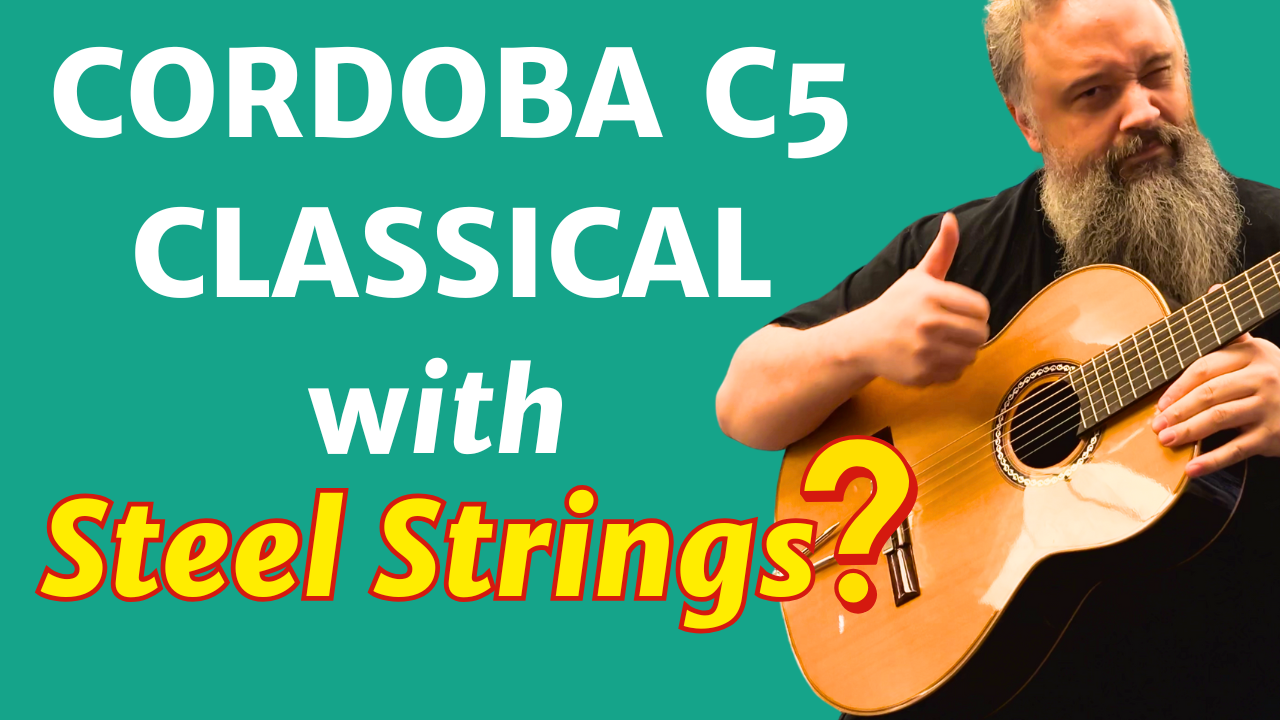
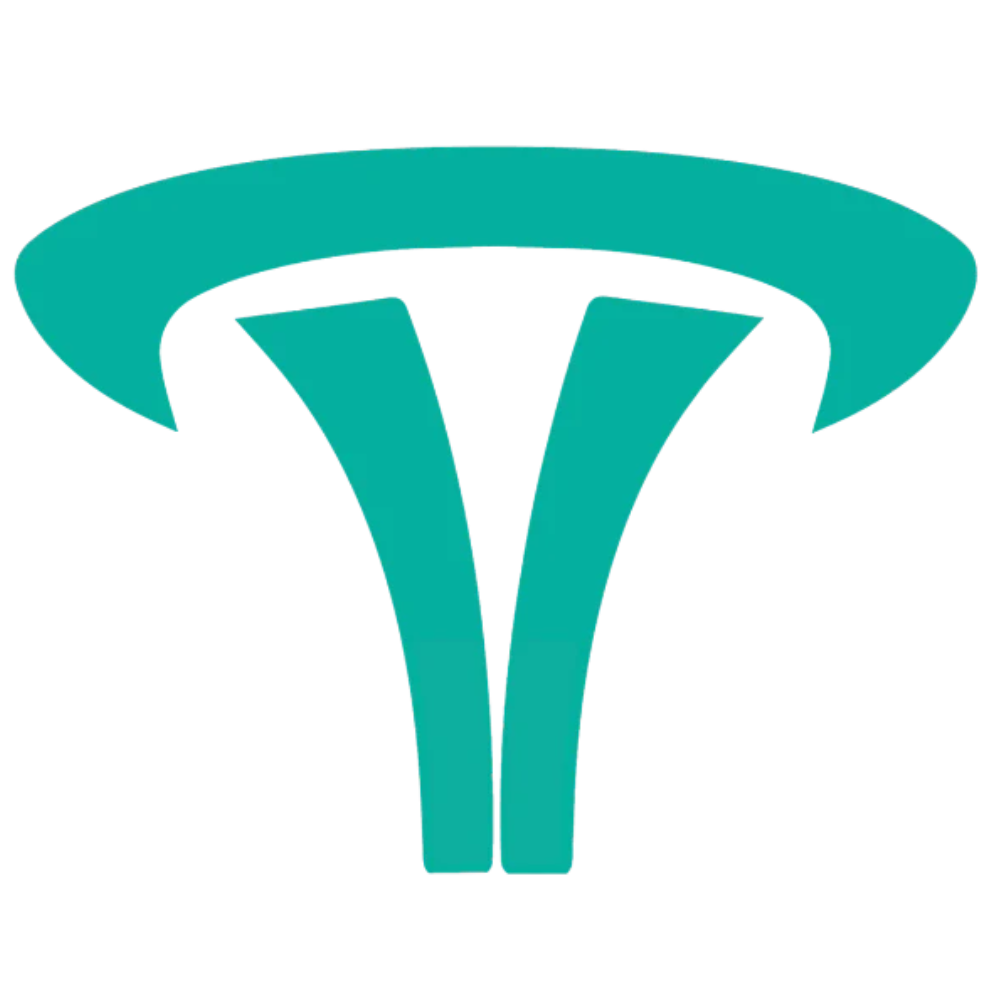
Steel Strings on a Classical Guitar?
Seattle guitarist, Bear Davis, plays a Turbo Guitar for the first time, a Cordoba C5 classical guitar with steel strings and the TurboTail.
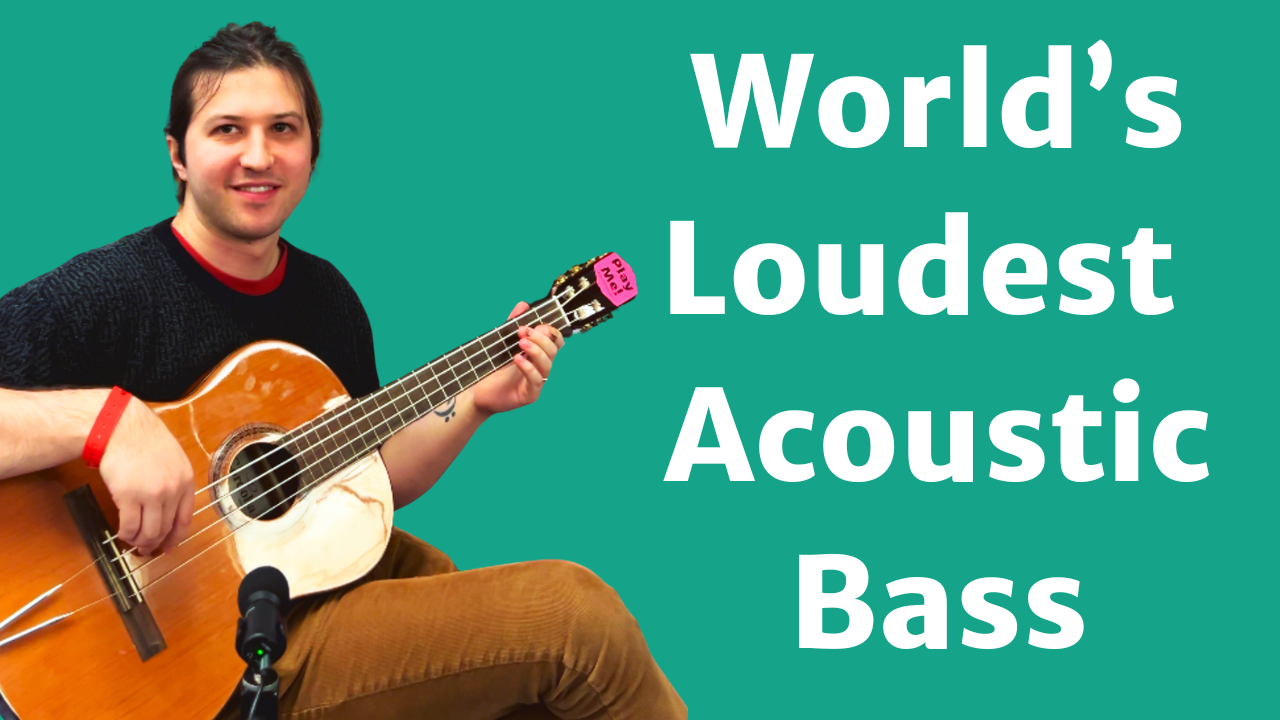
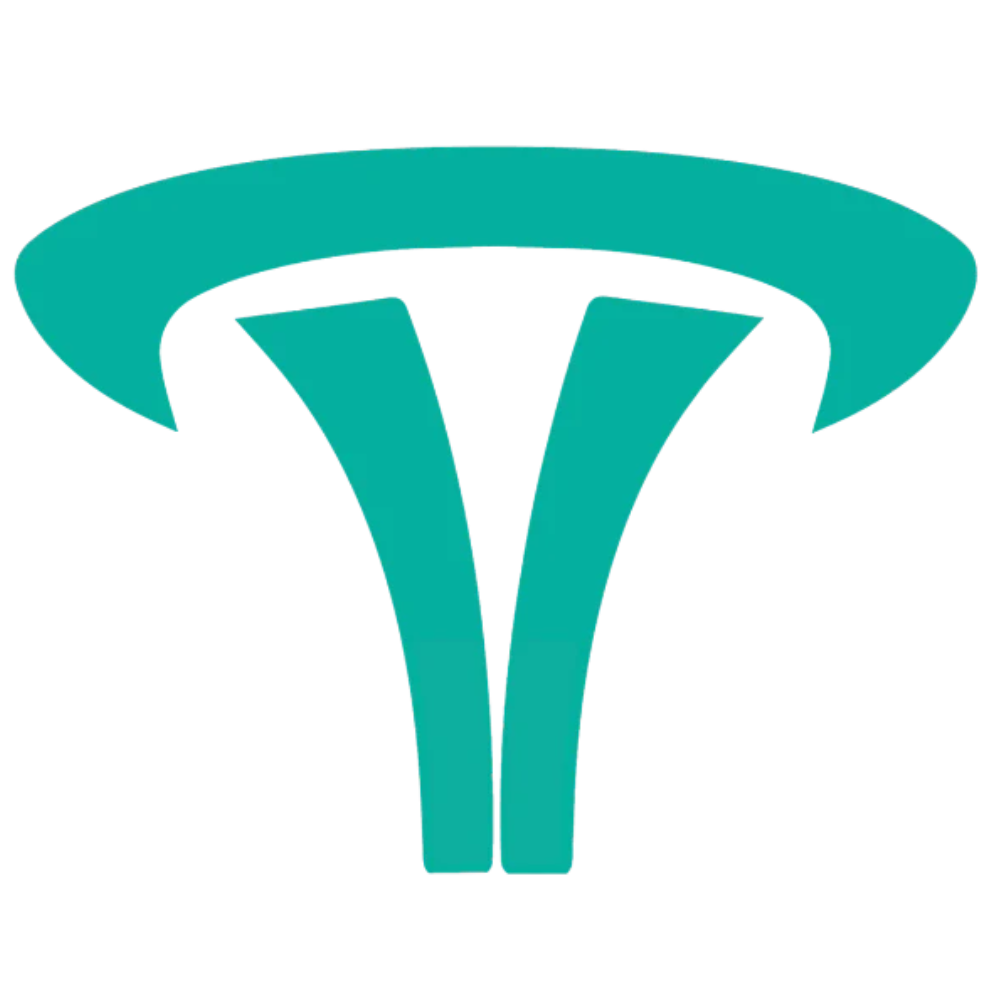
World's Loudest Acoustic Bass
In this video, Jesse is amazed by the volume and bass response of a Cordoba C5 classical guitar with bass strings and the TurboTail.
Our Free the Soundboard Devices
The TurboStrand & The TurboTail both free the soundboard by transferring string tension from the soundboard to the tail block. However, theTurboStrand hardware is less visible and was designed more for guitar builders.
Testimonials
"These days, I always use my Cordoba C5 classical guitar set up with steel strings and the TurboTail for my live solo gigs. It's just a lot louder than any of my other acoustic guitars and it sounds great."
— Mark Wand, professional guitarist, Seattle
“Incredible! This guitar breaks all the rules I’ve learned about how guitars are supposed to work.”
— Roger Ferguson, National Flat Picking Champion. He tested several Turbo Guitars at Wintergrass 2025:
“To my ear, both guitars have a similar tone that is really pleasing. The Cordoba is louder…interesting.”
— Bill, owner of Rosewood Guitar in Seattle (RosewoodGuitar.com) - After comparing a 1956 Martin 0 size to a Cordoba Cadete with steel strings and the TurboTail.
“That sounds amazing. There is so much projection. Do you have a card?”
— Alex De Grassi, fingerstyle guitarist, composer, and performer. Said after playing Cordoba C12 with steel strings and TurboTail at the 2023 GAL Convention.
“I’m interested. Here’s my card. I’ll be on a cruise this month. Call me next month.”
— Robert Godin said after playing Godin Motif and Etude guitars with TurboTail and steel strings. Mr. Godin is the founder and former CEO of Godin, Seagull, Simon and Patrick and Art and Lutherie guitar companies
“This could be revolutionary.”
— Bear Davis, song writer/guitarist and owner of Bear Den Studio (BearDenStudio.com)
“I have never heard a guitar of this size with so much volume and projection. It sounds great too.“
— Carl, guitar tech at Emerald City Guitars, Seattle. --After testing a small-bodied 24” scale Cordoba Cadet set up with steel strings and the TurboTail.
"It's Genius"
— Luca Canteri, professional guitar builder, Canary Islands, Spain (@ lcguitars.com)
“This is cool. Let me put you in contact with folks in the industry who can help you launch this.”
— Bruce Adolph: West Coast Guitar Shows CEO.
Limited Availability
Turbo Guitars and Basses For Sale
Do you want to own a Turbo Guitar or a Turbo Bass with a TurboTail or TurboStrand already installed? You can purchase one of our demo guitars or basses. Guitarists are amazed by the volume, bass response, and sustain of our guitars.
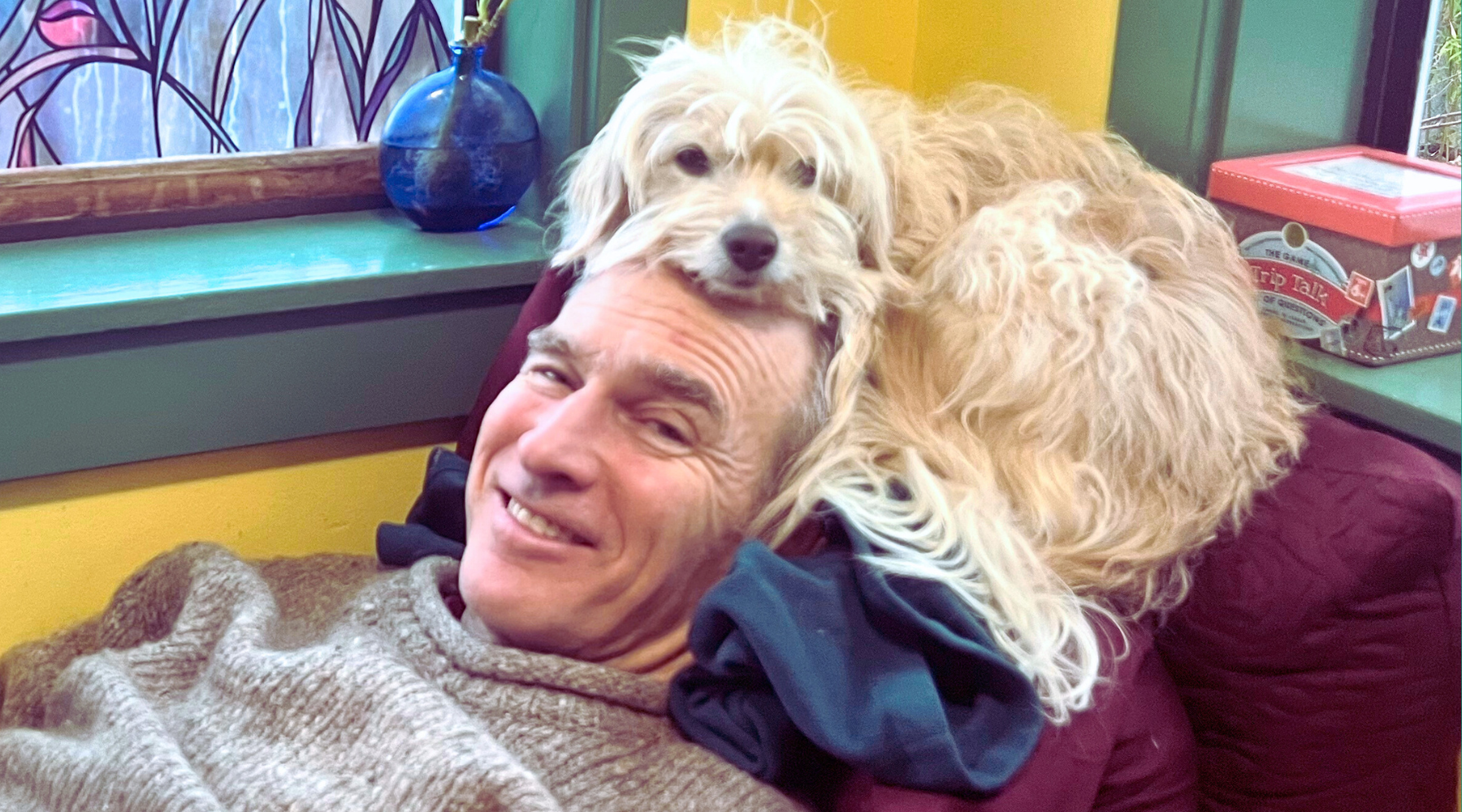
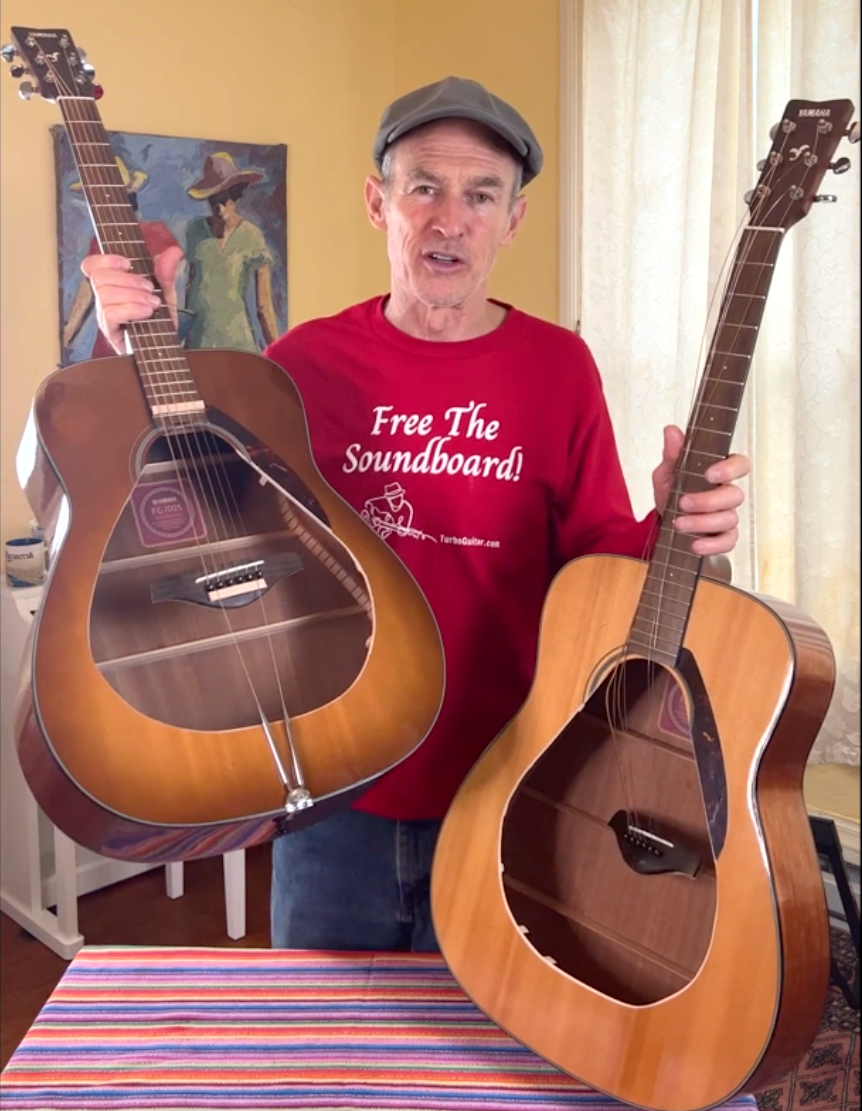
ABOUT TURBO GUITAR
I come from a family of visionaries and inventors. My grandfather spent his after-work hours developing a new refrigeration concept back in the early decades of the 20th century when cooling was still being done with ice. My dad had his first big success while still in his twenties, as part of a team that developed a frictionless rocket fuel mixer. I am a low-tech guy; I prefer simpler things such as guitars.
LATEST STORIES
Steel Strings on a Classical Guitar?
Can the TurboTail Impact Guitar Building?